对于深孔的铰削,也同样有一个排屑的问题。孔径在Φ30mm以下,应采用螺旋铰刀,以控制排屑方向,自动排出。当孔为通孔时,应采用左螺旋齿铰刀进行推铰,或用右螺旋齿铰也进行拉铰。对于盲孔,应采用螺旋β<30º的右旋齿铰进行推铰。当孔径D>30mm时,应采用浮动镗刀对孔进行铰削。浮动镗刀的结构如图16所示。
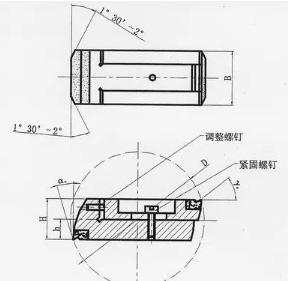
浮动镗刀是由两大件相配合结成,可根据孔径选用不同调整范围的镗刀,精确地调整所需尺寸。刀具制造时,它的前角γ0=0º这时可用来切削铸铁等脆性材料。由于它的刀刃高于中心h,所以它的工件前角γ0e=-值。当用来切削塑性材料时,这时它的前角就小了,就必须重新刃磨浮动镗刀的前角,使γ0=γ0e+η=18º~20º。可以用下式计算:tgη=h/√(D/2)²-h² (º)式中,D—工件的直径(mm);h—刀刃高于工件中心的高度(mm);η—刀刃高于工件中心时前角减小的值(º)。采用铰刀和浮动镗刀时的切削用量,Vc=5~10m/min,f=0.5~1mm/r。在切削的过程中必须有良好的润滑,并根据不同的工件材料,选用相应的润滑液。
铰削用量对于铰孔而言,铰削用量很重要,它对铰削过程中摩擦切削力,切削热以及切削瘤的形成和加工精度,表面粗糙度都有极大的影响,因此一定要合理加以选择使用。一是铰削余量,铰削余量不宜留的太大或太小,因为铰削余量留的太小,铰削时不易校正上道工序残留的变形和去掉表面的残留的缺陷,使铰孔的质量达不到要求。若所留的铰削余量太大,会加大每一个刀齿的负荷,破坏了铰销过程中的稳定性,且增加了切削热,是铰刀的直径膨大,孔径也随之扩张,切屑的形成必然呈撕裂状态,造成加工表面粗糙。二是机铰的切削速度和进给量,切削速度和进给量根据加工材料合理选择,进给量不能选的太小,太小时切削厚度可能小于切削刀齿小圆半径,铰削余量,切削速度,进给量这三个要素是互相影响。当切削余量较大时,切削速度,进给量就不能选的过高。反之,如果切削速度和进给量选取较小值时,则可适当提高切削速度。当然,为了更好地控制铰孔质量,除了铰刀几何参数及铰削用量外,可在铰削过程中,采用合理的切削液来排屑和冷却。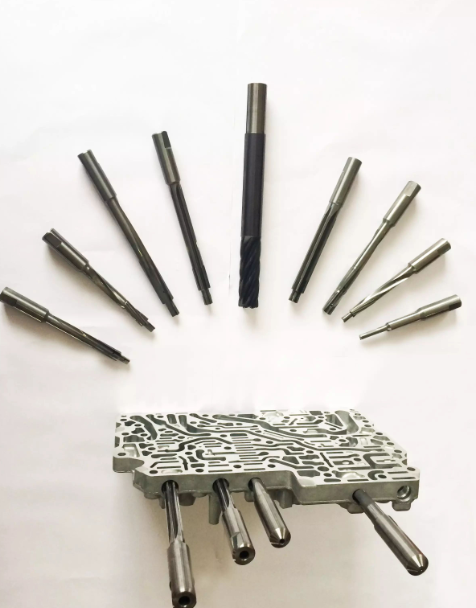
铰刀 用于铰削工件上已钻削(或扩孔)加工后的孔,主要是为了提高孔的加工精度,降低其表面的粗糙度,是用于孔的精加工和半精加工的刀具,加工余量一般很小。铰孔的质量好坏取决于铰刀本身的精度和表面粗糙度,因此铰刀几何参数的合理选择,决定了被铰孔加工的质量好坏,第一铰刀的直径,它是根据加工孔的公称尺寸和公差以及在铰销过程中被加工孔的扩张量或收缩量决定的。第二铰刀齿数,铰刀齿数3个刃、4个刃、6个刃、8个刃。铰刀已有上百年的制作,工艺技术比较成熟。经过了很多实践经验、开发出、标准DIN标准、其中之一二材质为HSS-E 、VHM、分为直A和直B型铰刀。直A螺旋度7度 直A型铰刀0.95mm--1.7mm一下是3个刃1.8mm---2.6mm是4个刃 、2.7mm—13mm以上是6个刃、14mm—20mm是8个刃。合理的螺旋铰刀大小尺寸有利于加工工件的精度、有些铰刀制造不合理的韧带会影响到铰孔的光洁度和精度。有铰孔的精度越高,但是减少了容屑槽,再切销时,刃的多少根据铰刀的尺寸大小而定、刃口过多不易切屑不容易排出,特别是在铰深孔和切削余量大时,因容屑槽被切屑堵塞,切削液就流不进去,致使铰刀和工件因产生热量而变形,影响加工质量。所以铰刀的齿数一般都选用合理的铰刀厂家。要看铰刀的刃口有没有锯齿状。如有锯齿状说明铰刀在制作过程中砂轮放的过粗。但刃倾角能使切削过程平稳,提高铰孔质量。在铰削韧性较大的材料时,可在铰刀的切削部分磨出=15°~20°刃倾角,这样可使铰削时切屑向前排出,不致于划伤已加工表面。在加工盲孔时,可在这种带刃倾角的铰刀前端开出一较大的凹坑,以容纳切屑。
关于铰刀切削 铰孔、铰刀切削速度快好还是慢好一般铰孔的一个原则是低转速,高进给,转速尽量要低,进刀量要适当快一些。转速和工件的材料,铰刀大小,加工余量粗糙度要求都有关系,一般钢件采用高速钢刀具切削速度为20米每分钟,转速N=1000*v(切削速度)/πD,如10的铰刀在20米切削速度下转速N=1000*20/(3. 14*10)≈640转/分,进给量F=走刀量(MM/转)*N(转速)如,铰孔走刀量为0.2/转,那么F=0.2*640=128MM/分。不同的铰刀有不同的加工方式。从上公式可知,在满足质量要求的前提下,尽可能选择最经济的参数。不过在铰圆的前提下留量越少越好,转速低粗糙度越好,进给量越慢粗糙度越好,注意要加冷却水及冷却油。铰刀国际公差H7 及0.007μ的铰刀。一般可以满足大众孔加工精度只要求。